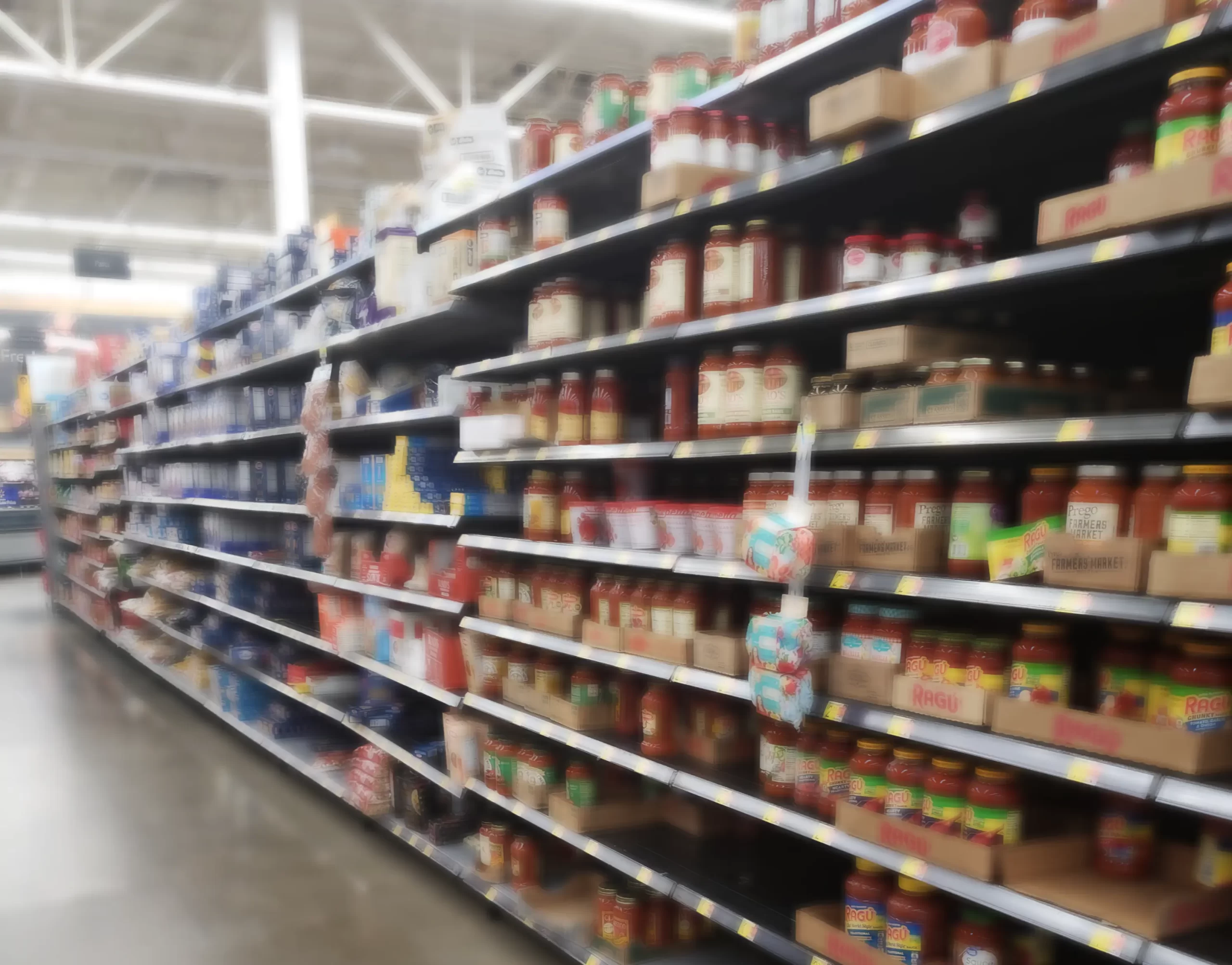
Inventory Management Planning
The inventory management is generally performed & managed by the Supply Chain Management (SCM) function of a company. This is one of the critical activities and the health of a firm is usually determined by the level of inventory maintained at any point of time. The main mantra is to keep an optimum balance of inventory. As the very term ‘optimum’ suggests that there should not be excess inventory in the company books of accounts and at the same time there should not be any shortage in stock. In fact, the objective of inventory management is to ensure the target level of customer service, ensure cost-efficient operations and reduce and optimize inventory investment. The SCM head has a very big role to play here as he is designated to lead the inventory management.
In a service sector like telecom service, inventory management is mission-critical. In case of any deviation in stock level, it will directly impact customer experience which will directly have a negative impact on business revenue and customer satisfaction. The telecom network needs to be up and running 24*7*365 and hence an optimum balance of serviceable equipment must be maintained at all times and all hours. For instance, if a site is down, at a location, a huge number of customers get impacted as they cannot initiate or receive voice calls due to the outage. Hence, the service engineer needs to immediately visit the site, take the required spare part from stores under SCM, and replace the faulty part. In no way, an engineer can wait for the spare part, and hence an optimum level of stock of these spare parts is a must. The above case scenario simply shows how important is to maintain the optimum level of stock. These spares are very costly and hence accumulation of spares will directly negatively affect company revenue. Again a very low level of stock or zero stock or poor warehouse management could be disastrous.
Inventories can broadly be classified into 5 types however this classification depends upon the type of business. Generally, the 5 types of inventories are – Raw materials inventory, Maintenance, Repair & Operating (MRO) inventory, Decoupling inventory, Work In Progress (WIP) Inventory & Finished Goods Inventory. Good warehouse and inventory management will effectively classify these categories.
Raw materials
The materials which are required to produce finished goods are called raw materials.
The raw materials constitute a very important aspect of the overall functioning of inventory management. The SCM lead must ensure that an optimum level of raw material is always available in stock so that the finished goods are always available as per the requirement of the customer order. A very high number of raw material availabilities would result in unnecessary excess accumulation of inventory and will hit the profitability index. At the same time shortage of raw materials will affect production and hence the profitability and customer satisfaction will be negatively impacted.
For example, if we analyze the mobile phone industry, would immediately get the importance of raw materials like any other sector.
There are some mission-critical components that constitute the manufacture of Mobile phones.
For example, earphones, microphones, the LCD screen, keypad, IOS software etc should always be available in optimum numbers during the production phase for the final finished product which in this case is a mobile phone. As per the list mentioned above, there are hardware and software components. The software components like IOS, basic applications etc should be stored at a centralized server so that the same can be retrieved or installed in mobile phone hardware components during production. Again, the hardware components should be in adequate and some 5% additional reserve in stock should be maintained in case of new spare defective cases or physical or environmental damage during the storage in the warehouse.
Again if we take the case of final products like generating energy, Electricity, boilers etc, coal happens to be the most important raw material which is available in nature. Hence the availability of coal must be ensured for generating electricity and usually, the plants are built close to the coal production zone so that there is no shortage of availability of raw materials. Also, thousands of tons of coal are stored in the warehouse to ensure ready availability of these raw materials, else there would be a direct impact on power generation resulting in a negative impact to the GDP of a nation.
Maintenance Repair & Operation (MRO)
MRO inventory management stands for maintenance repair & operation inventory. Technically, these are the materials, equipment, and supplies used during the entire work process till the final product is manufactured. This can be maintained in numerous manners such as personal warehouses or cloud inventory.
These are mainly the consumable items and as per the finance terminology, the cost usually goes into OPEX (operation expenditure) head. Below are some of the typical examples of MRO items that are generally in use during the production activity till the final material is made ready.
Personal Protective Equipment’s (PPE) – Typical examples are gloves, masks, safety glasses, helmets etc. During this pandemic scenario, more emphasis is laid on PPEs like face-shields, sanitizer etc, and hence the OPEX expenditure increased.
Cleaning ingredients like disinfectants, brushes, special containers etc as maintaining the basic hygiene at the production zone is of utmost importance and more so during the ongoing pandemic situation.
Office stationeries like notebooks, pens, post-its etc which are extensively used for documentation and marking the work progress in a systematic way.
Electronic gadgets like desktops, laptops, printers, scanners etc for digitally recording the progress and maintaining the artifacts during the production period. This is extremely important as regular updates need to be communicated over digital media to top management for work progress tracking. Along with hardware, relevant software tools are also used like Microsoft Project , Visio etc for data updates and sharing.
Lubricants, valves, bearings etc are also used during the production stage as consumables.
Hence MRO plays a vital role during the entire process and should be planned for overall 100% success for finished products in time.
Work-in-progress (WIP)
The time required to assemble the raw materials till the completion of finished goods is technically termed as WIP or work in period phase.
The target timeline is usually set for the WIP period by the SCM head so that there is no deviation. In fact, the WIP period should be set to an optimum duration of timeline and at the same time good quality of finished goods is also to be ensured. Usually, multiple quality checks are done during the WIP phase so that the quality and the set timeline work hand to hand. A strict tracking is done for the progress of work during the WIP phase and in many companies’ software tools are used to track the daily flow of work. A red flag is set immediately in case of any slowdown and analysis done by the top management. Subsequently, a new timeline is set so that on any condition the final finished goods timeline is not hampered. More manpower, adequate raw materials etc are pumped in to ensure the timeline. WIP in the pandemic situation – Last 2 years the WIP period had been adversely affected. Due to the covid situation, the availability of manpower was impacted and at the same time, the raw material shortage and transport unavailability affected the production time. In many cases, the WIP period had to be extended resulting in a huge delay period for the final production. However, in a normal scenario, the timeline for WIP must be strictly monitored and the deadline must be met for the readiness of finished material.
De-Coupling Inventory
This is a concept in which the manufacturer set aside a buffer stock of raw materials which could be used in case of shortage during the WIP stage to finished goods. This is extremely important, and the buffer inventory must be planned well in advance. For example, in case oil and natural gas requirement as raw materials during the WIP stage, these raw materials rise and fall quite abruptly as per the global changing market environment and hence maintenance of reserve stock is a must.
The de-coupling inventory is also considered a very important part of successful inventory management. The decoupling products are totally kept aside inside the warehouse so that the same is not used during the production phase. This should only be used under extreme emergencies, in case of acute shortage of regular raw materials, and post approval of the SCM head.
Finished Goods Inventories
The end of the supply chain management and the ready products which are to be sold to customers. The finished manufactured stage goods, now, are ready to be sold to the prospective customers and post selling profit realization takes place. This can be maintained in numerous manners such as personal warehouses or cloud inventory. This is where a point of sale inventory management software such as Alnicosoft is particularly helpful
The 80/20 rule can be linked to inventory which states that companies can earn roughly 80% of their profits from 20% of their products. This simply exemplifies the mission critical role of inventory management in successful running of a business.
There are 5 main principles that guide inventory management and all these 5 principles should be followed. The 5 principles are demand forecasting, warehouse flow, inventory turns/stock rotation, cycle counting, and process auditing.
It is to be noted that post in-depth studies it has been found that Inventory management can be effectively controlled using the Alnicosoft Inventory module. While developing the POS, all inventory management algorithms have been duly considered by the expert team. Below are the salient features which make the module unique and stand out from the rest of POS.
- Group products by Product Category for easy tracking of products.
- Update Stock using Inventory services.
- Manage inventory levels for each store at any location.
- Set discounts by product and by store effortlessly.
- Efficiently configure tax rates to comply with your state, county, and/or resident jurisdiction laws.
- Provision to enter product stock location of each store.
The detailed modules can be studied in depth by visiting the official site www.alnicosoft.com. Overall this POS application is cost-effective and all aspects of inventory management are effectively covered giving the desired value to the customer.
The Alnicosoft – An ultimate advantageous POS and Inventory Management System for Customer Satisfaction & Retention. Try now.